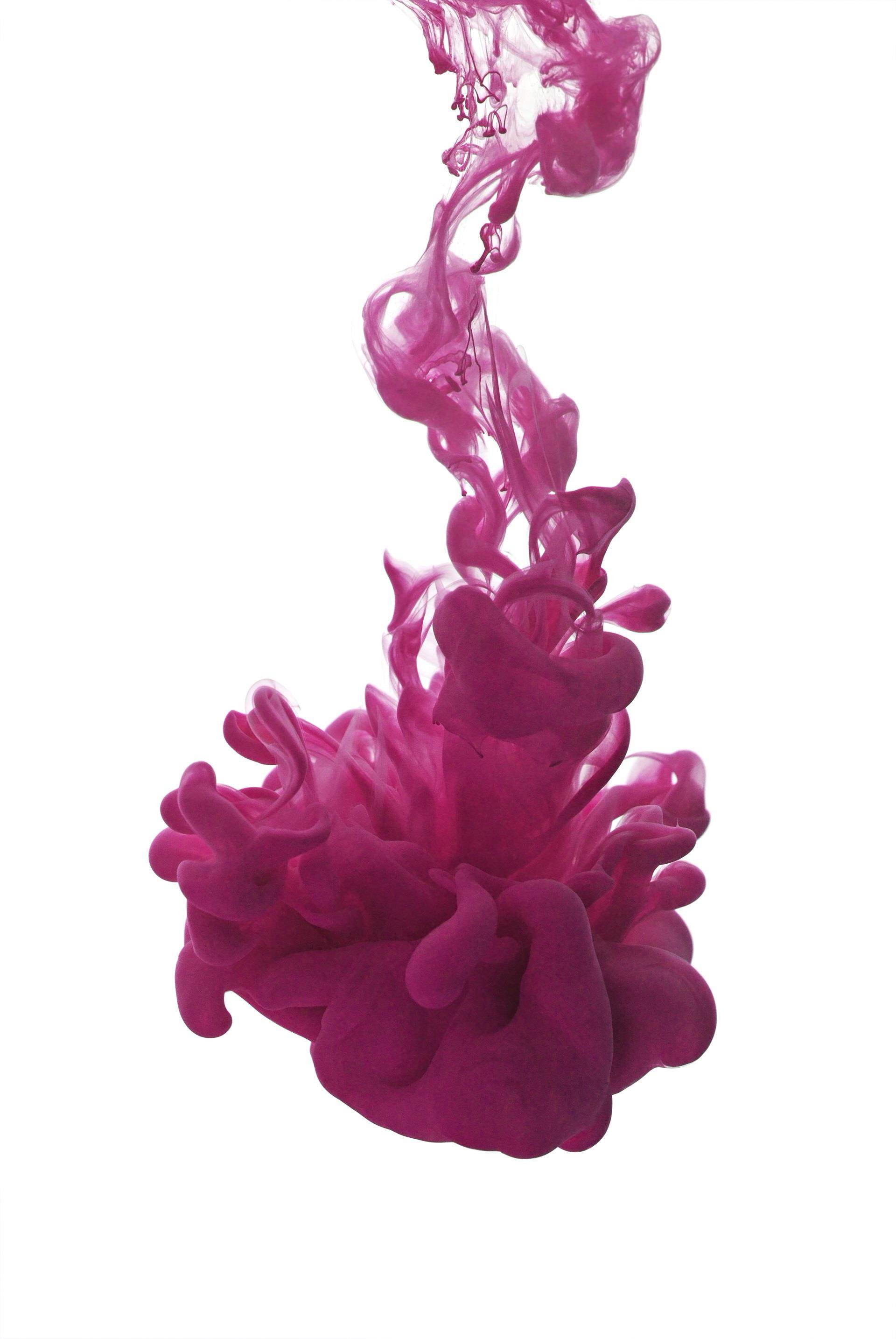
Dispersants
Dispersing agents promote the even and stable suspension of relatively small particles in a given medium. The optimum dispersant(s) required for a particular molecule depends on its size and charge distribution. Croda offers a range of chemistries and technologies that are compatible with a wide variety of formulation systems. Our dispersion technologies are successfully used in a range of applications and with our knowledge can help find the right dispersant for your formulations.
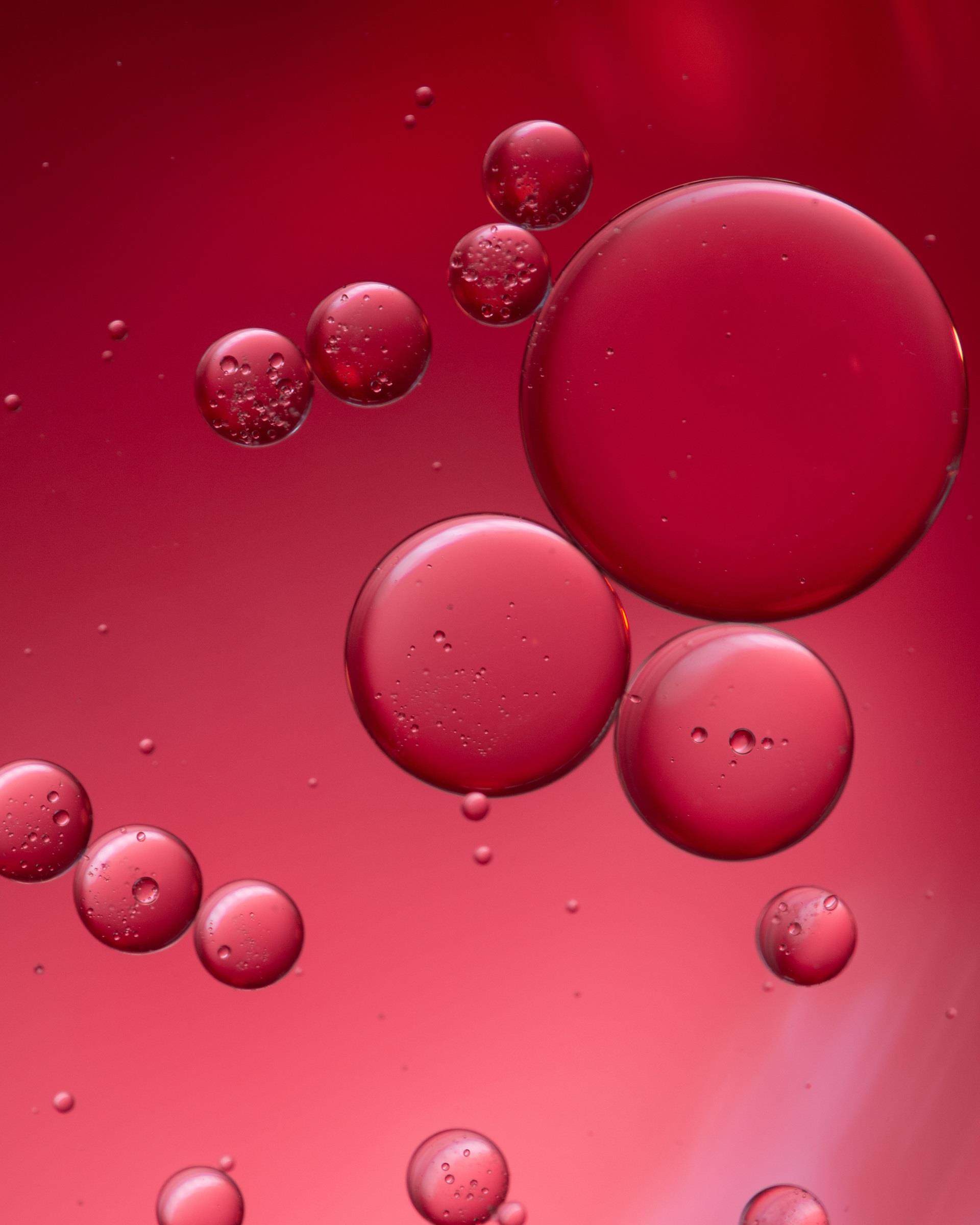
The dispersion process
Wetting
Wetting is the ability of a liquid to maintain contact with a solid surface. The wetting of particles is essential for them to be finely dispersed in a liquid. Any air entrapped in the powder must be fully removed and the particle completely surrounded by the liquid medium that the particle is to be dispersed in, this stage is often referred to as milling. For the liquid to wet a solid, the surface tension of the liquid must be lower than that of the solid. A liquid with lower surface tension wets pigments better than one with a higher surface tension. It is important that the wetting/dispersing additive is compatible with the solvent(s) used in the continuous phase.
Dispersion stability
Stability is key to maintaining a fully dispersed solution. There are several ways in which this can be achieved:
- Colloidal stability - prevent coagulation through inter-particle repulsion;
- Kinetic stability - slow down sedimentation by increasing velocity of continuous phase; and
- Thermodynamic stability - make it solid by creating a network structure.
Colloidal stability
To maintain stability through Brownian motion, we must prevent particles sticking together when they collide.
- This can be achieved by increasing the charge associated with the particle (i.e. Zeta potential).
- Zeta potential is a physical property which is exhibited by any particle in suspension.
- It can be used to optimise the formulations of suspensions and emulsions.
- The understanding of the zeta potential of a system enables a chemist to produce better and more stable formulations.
- There is an energy barrier resulting from combination of the attractive and repulsive forces prevents particles approaching each other closely.
- So long as the kinetic energy of a particle does not exceed this barrier, coagulation should not occur.
Figure 1: The energy of a system must exceed the energy barrier for agglomeration to occur. The energy barrier can be greater if Zeta potential between particles is maximised.
Kinetic stability
For occasions when gravitational forces dominate over the Brownian forces we must look to another approach to improve stability. This can be achieved by:
- Increasing low shear viscosity;
- Gelling particles into a solid matrix;
- Decreasing particle size; and
- Matching density of dispersed and continuous phases.
Thermodynamic stability
For a particle to stay suspended in a gelled system, the yield stress of the gel must excveed the gravitational force acting on the particle. A material with a yield stress will stretch out like an elastic material, until the yield point and then begin to flow.
Polymeric surfactants
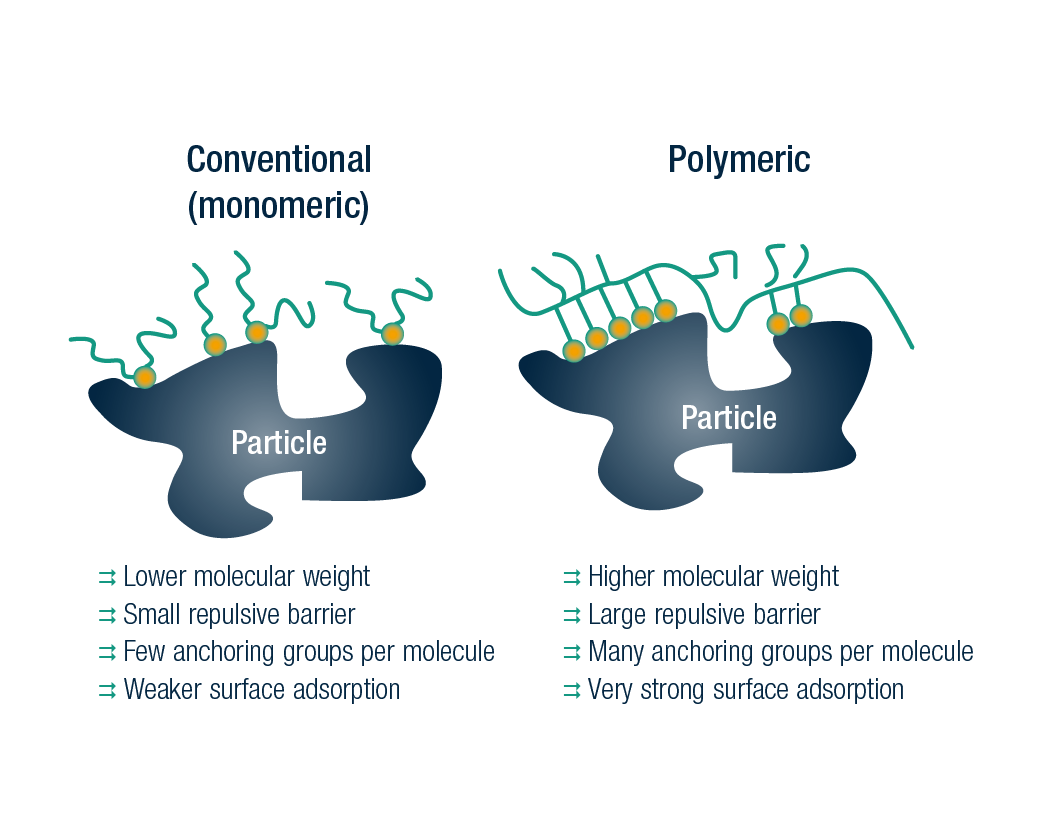
The diverse range of particle types and sizes that need dispersing means that in order for us to make appropriate recommendations it is important to understand what is required in order to create a good dispersion.
The right solution will depend on many factors such as:
- Particle size / shape
- Particle density
- Surface charge of particle
- The solvent the particle is to be dispersed in
- Desired solids loading of dispersion
- The pH of the system (if aqueous)
- What kind of doping is present (often the case in certain applications).
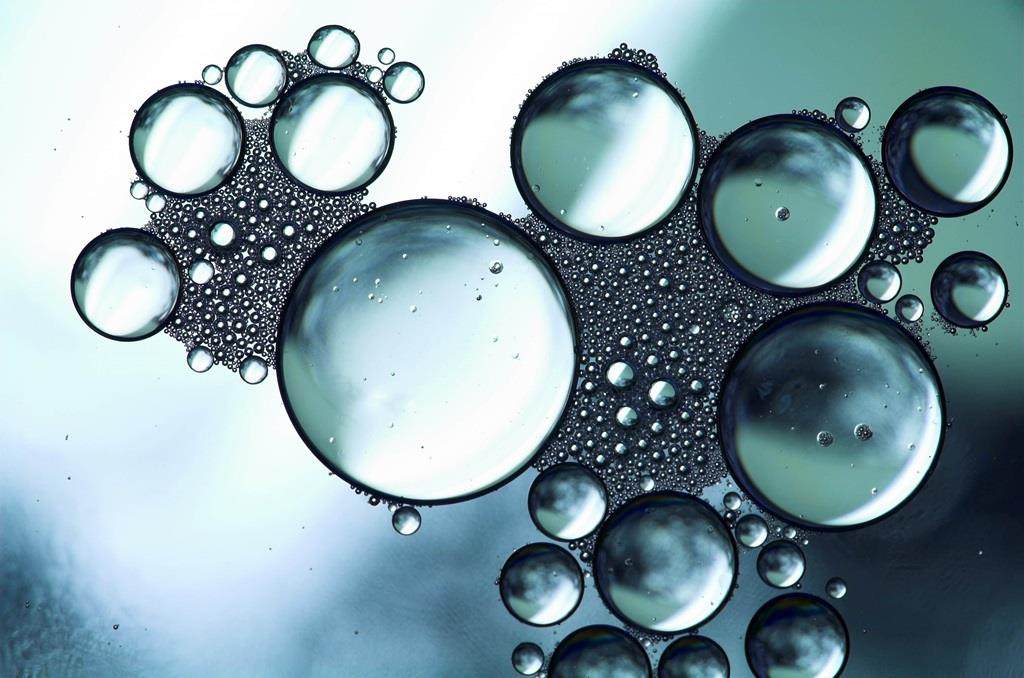
Polymeric surfactants and dispersants
For specialist and demanding emulsion and dispersion applications, customers should consider our range of polymeric surfactants and dispersants. These proprietary polymers provide an extra degree of flexibility in formulating. They work to stabilise the emulsion, preventing the coalescence of emulsified oil or water droplets under more extreme conditions. Some specific benefits of the range are:
- versatility;
- electrolyte stability;
- thermal stability;
- shear stability; and
- high performance at low treat rates.
Our recommendations
For specific demanding emulsion applications, customers should consider our range of polymeric surfactants. These proprietary non-ionic polymers provide an extra degree of working flexibility in formulating, to stabilise the emulsion systems by preventing coalescence of emulsified oil or water droplets under more extreme conditions.
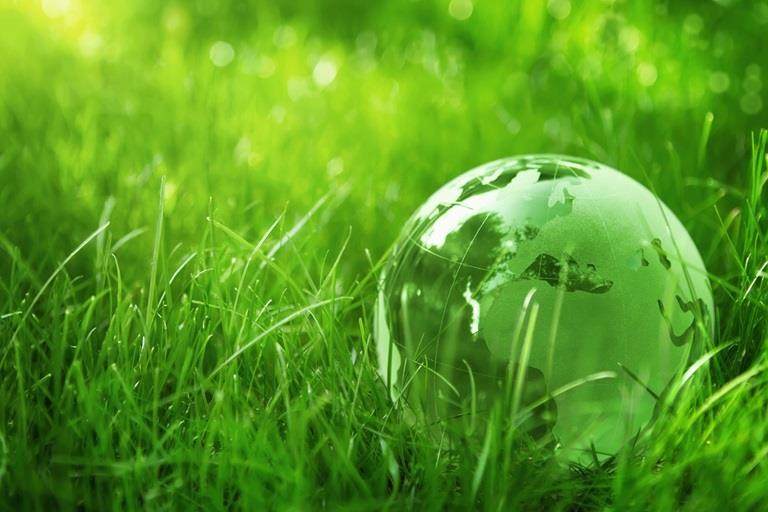
Hypermer 1599
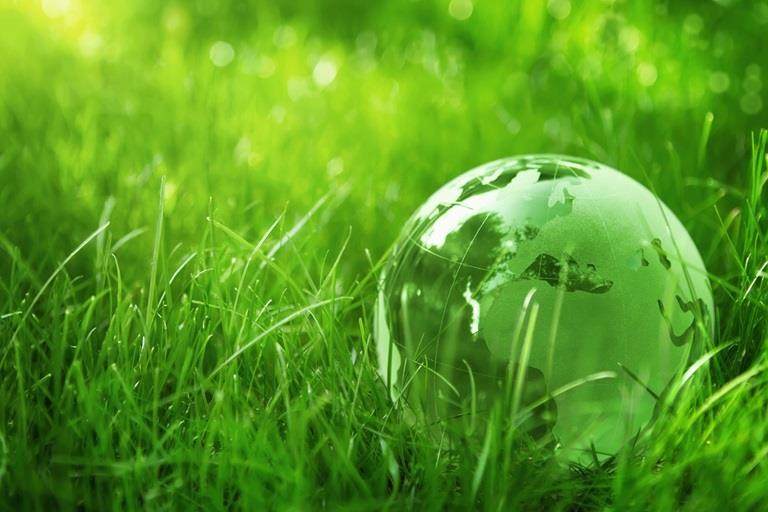
Hypermer B261
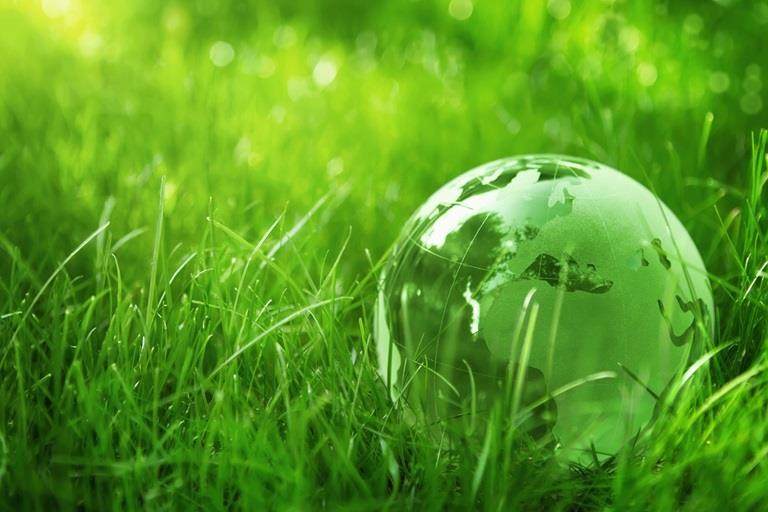
Hypermer™ LP1
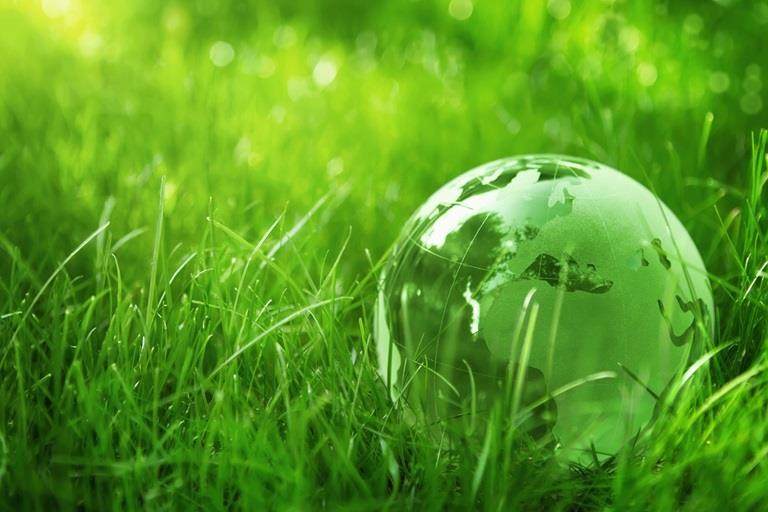
Zephrym™ 3300B
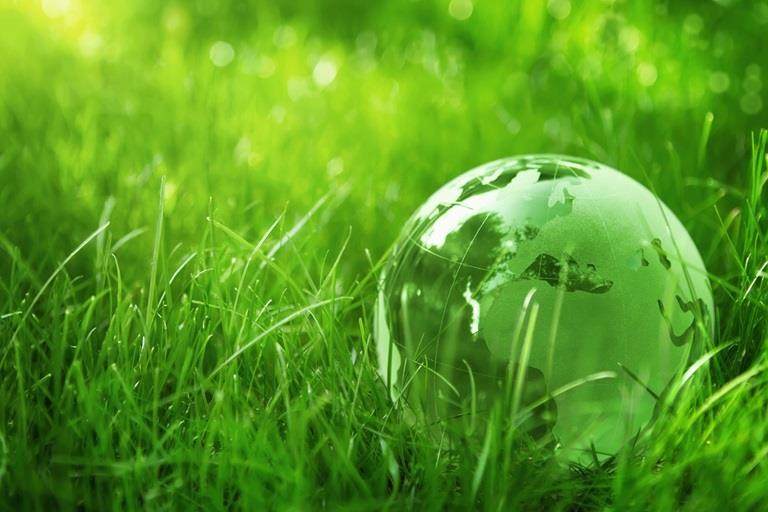
Zephrym PD3315
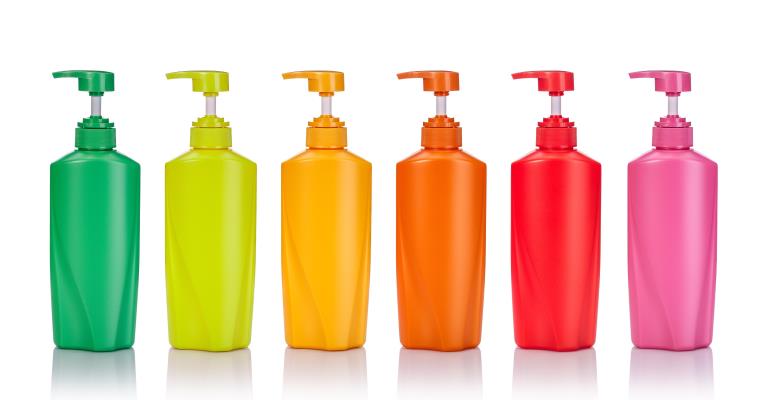